Introduction
Bird strikes happen most often during takeoff, landing or low altitude flight. However, bird strikes have also been reported at high altitudes, some as high as 6,000 to 9,000 m above the ground. The point of impact is usually any forward-facing edge of the vehicle such as a wing leading edge, nose cone, jet engine cowling or engine inlet.
As the bird strikes a fan blade, that blade can be displaced into another blade and so forth, causing a cascading failure. Jet engines are particularly vulnerable during the takeoff phase when the engine is turning at a very high speed and the plane is at a low altitude where birds are more commonly found.
The force of the impact on an aircraft depends on the weight of the animal and the speed difference and direction at the impact. The energy of the impact increases with the square of the speed difference. Hence high-speed impacts, as with jet aircraft, can cause considerable damage and even catastrophic failure to the engine.
Geometry and mesh
Since the crash analysis is highly nonlinear, an explicit finite element scheme had to be used. As we have already discussed in other case studies, the computational expanse depends greatly on the number of elements as well as the size of the finite element. To keep the model relatively simple, we have modeled the fan blade with shell elements. Shell elements had variable thickness throughout the fan blade.
For better presentation, all the fan blades are modeled, although only three of the blades were deformable. Other fan blades are modeled as rigid. Since the rigid elements are far less computationally expensive this simplification also improved model performance. The model of the fan blade can be seen in Figure 1
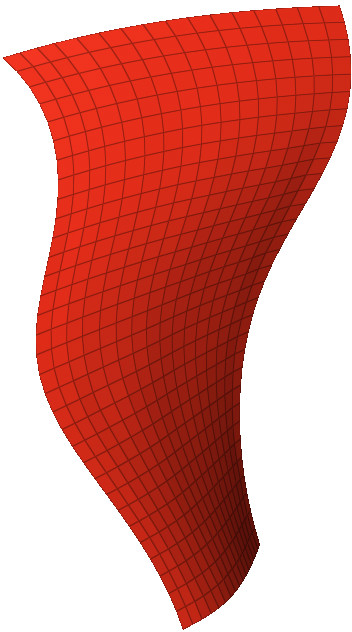
Another goal was to adequately model the “bird”. During the impact, the specimen undergoes severe deformations which would not be possible to model with the conventional finite element method. For this, and similar purposes entirely different line of elements was introduced. The most well know are SPH (Smooth Particle Hydrodynamics) and ALE (Arbitrary Lagrange-Eulerian) elements. These elements have different formulations and are appropriate for extremely large deformations.
The arbitrary Lagrangian-Eulerian is a finite element formulation in which the computational system is not a prior fixed in space (e.g. Eulerian-based finite element formulations) or attached to the material ( Lagrangian-based finite element formulations). ALE-based finite element simulations can alleviate many of the drawbacks that the traditional Lagrangian-based and Eulerian-based finite element simulations have. When using the ALE technique in engineering simulations, the computational mesh inside the domains can move arbitrarily to optimize the shapes of elements, while the mesh on the boundaries and interfaces of the domains can move along with materials to precisely track the boundaries and interfaces of a multi-material system.
SPH is a meshfree method, which makes it ideally suited to simulate problems dominated by complex boundary dynamics, like free surface flows, or large deformation. SPH can be easily extended to a wide variety of fields, and hybridized with some other models, as discussed in Advanced techniques and applications.
In our analysis, the standard bird specimen was modeled with SPH elements. The SPH model of the bird specimen can be seen in Figure 2
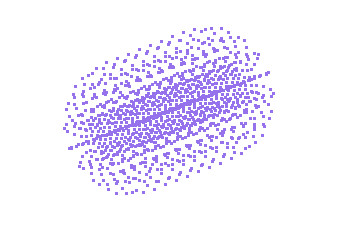
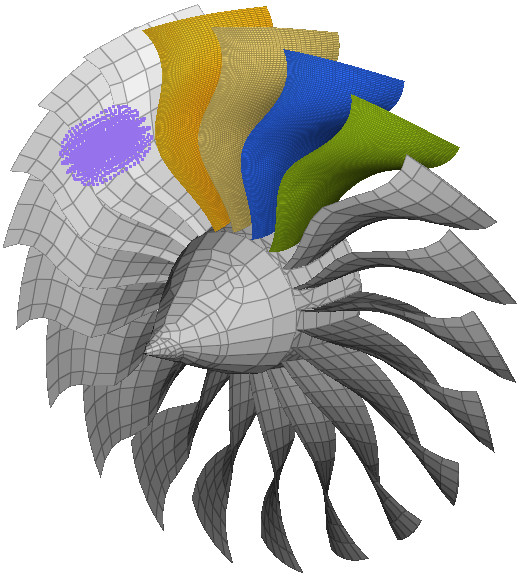
Results
Prestress calculation
Since we do not want to simulate the engine run-up, a prestress analysis was carried out. This analysis represents the stress conditions in the structure when exposed to the centrifugal force. This prestress state was imported into the first step of the explicit analysis. The results for the prestress can be seen in Figure 3
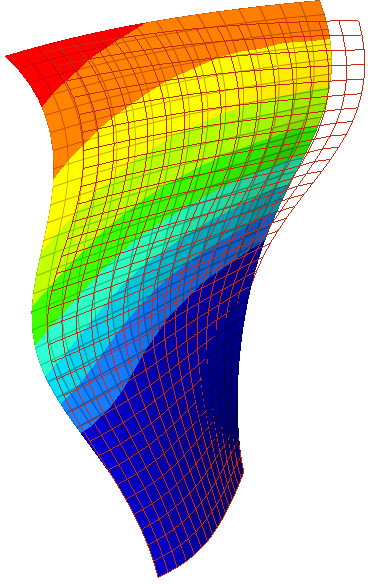
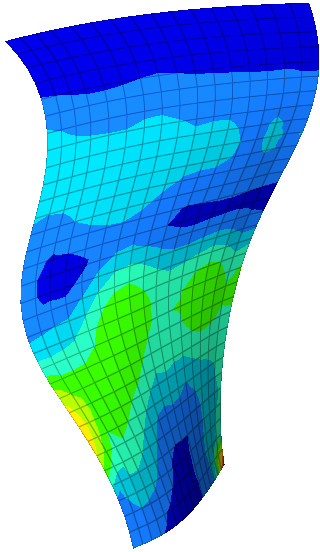
Bird strike analysis
During the bird strike event, we were most interested in the structural behavior of the fan blades. We can observe, displacement, stress plastic strain and also damage.
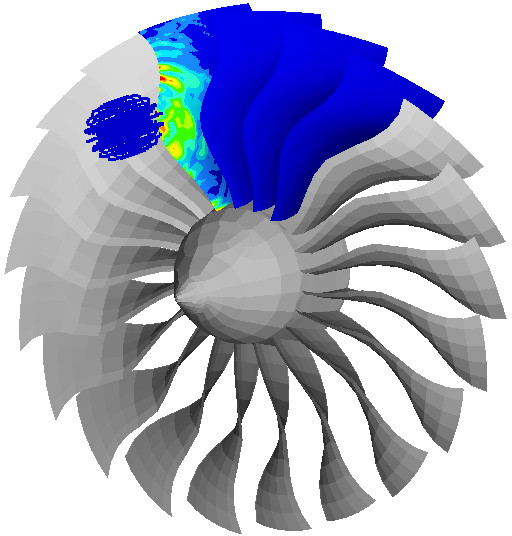
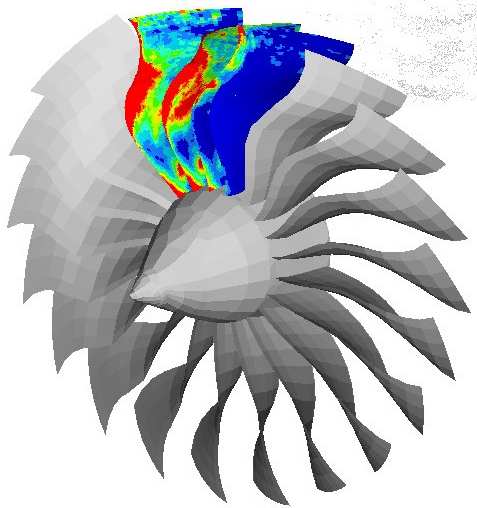
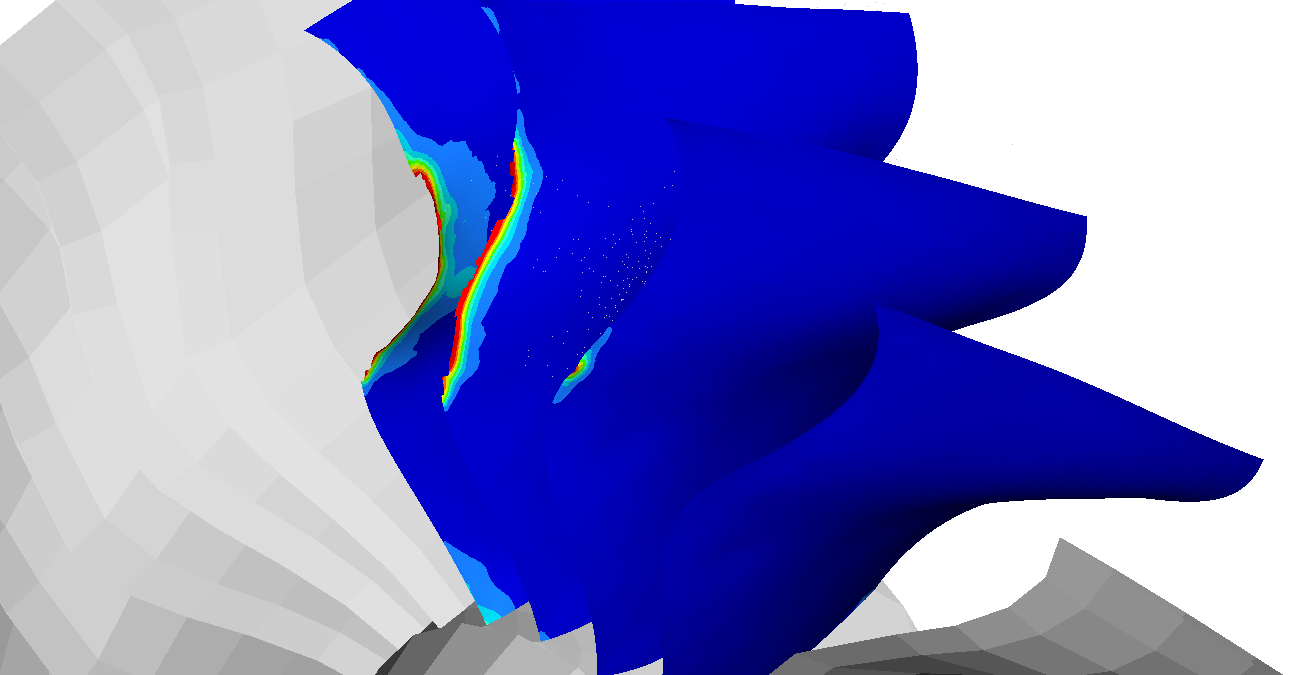