OUR SERVICES
Numerical simulations
Numerical simulation can give us an incredible insight in the behaviour of our product. With the use of Finite Element Analysis, Computational Fluid Dynamics and other simulation methods we can study the real-world environment and adapt our design faster. This results in a more reliable and cheaper product with a faster time to market.
Get in touch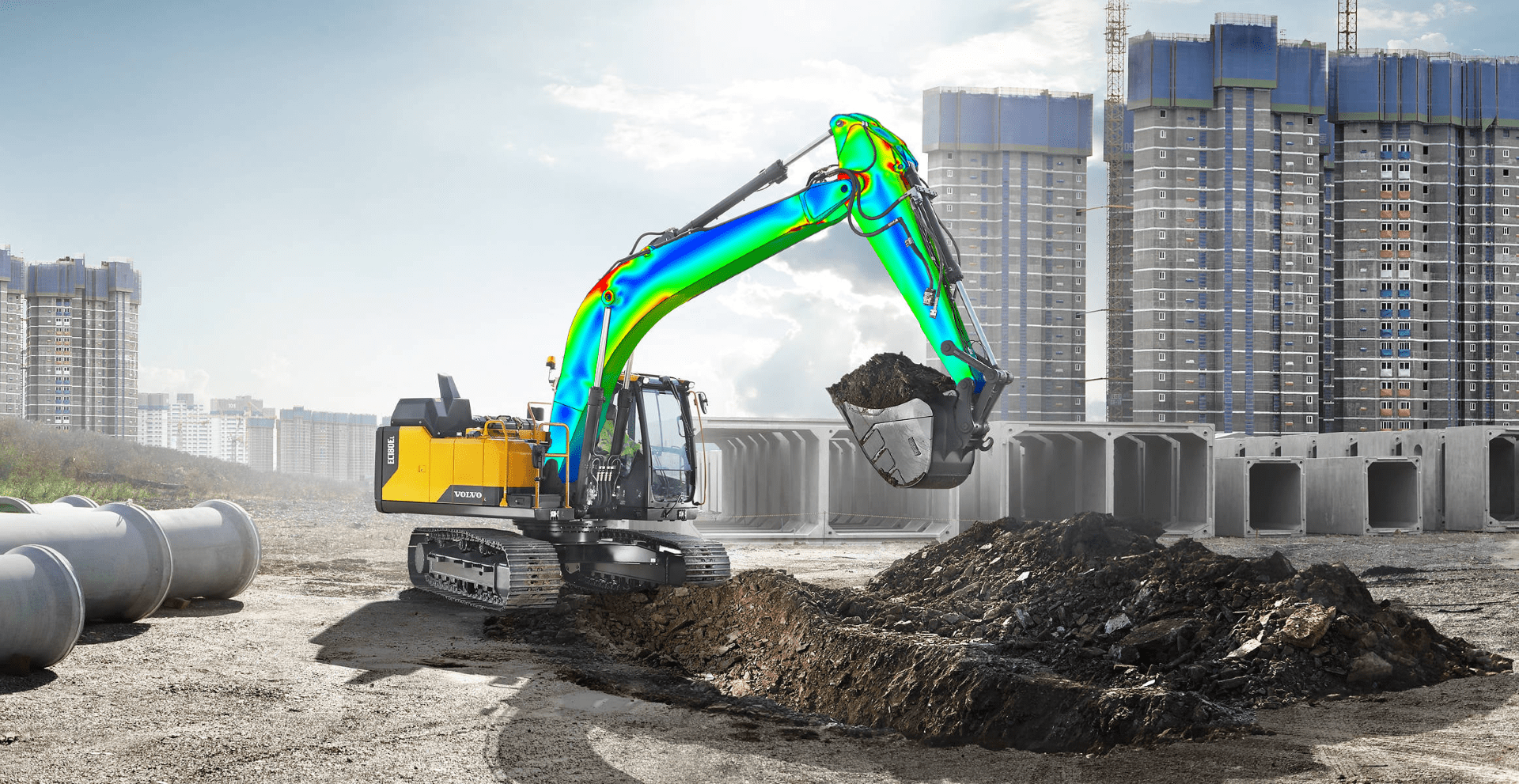
Types of numerical simulations
Structural analysis
Our analyses
- Nonlinear analysis (Complex nonlinear problems including nonlinear contact, material properties and large deformations, buckling, creep, etc...)
- Structural analysis (Code compliant analysis of civil and industrial structures.)
- Pressure vessel analysis (ASME Section VIII Division 2)
- Pipeline stress analysis (Welding stresses with safety assessments, ASME B31.3)
- Thermo-mechanical simulations (Thermo-mechanical loads, expansion of materials, residual stresses)
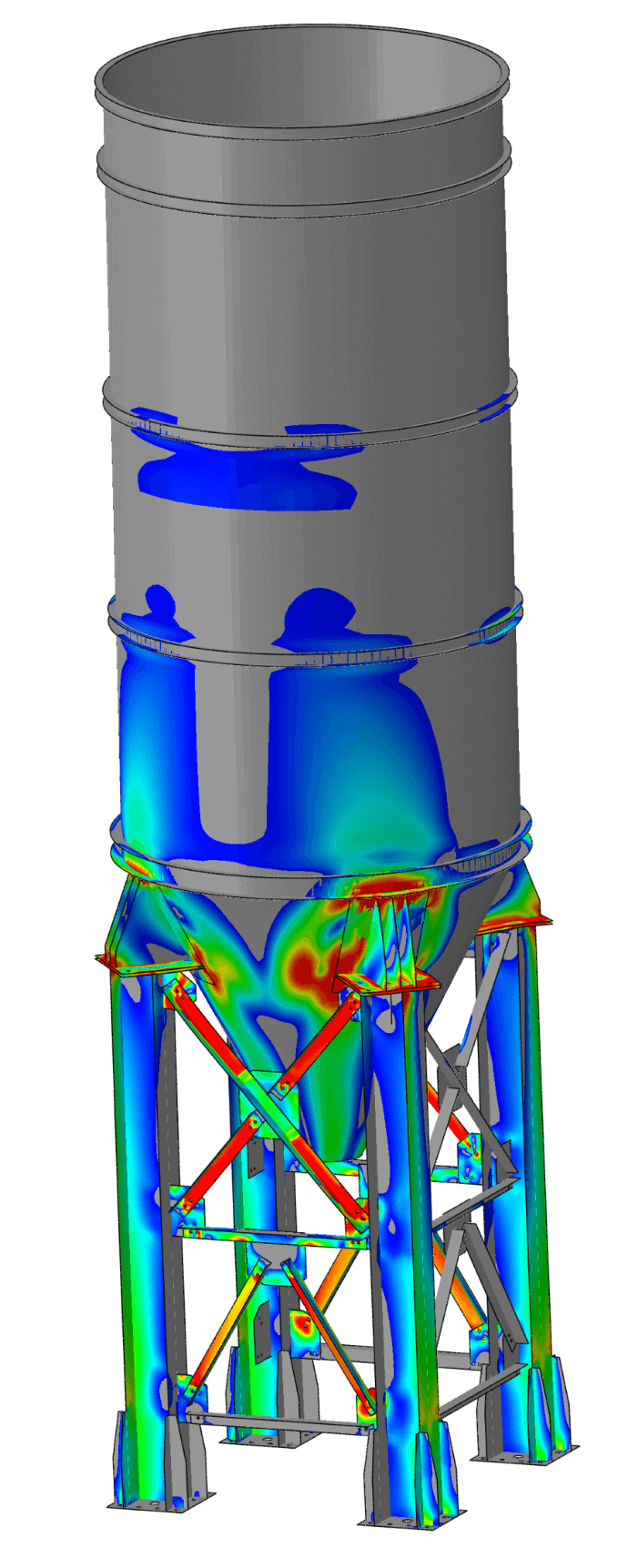
Dynamic analysis
Our analyses
- Multi-Body Dynamics (Complex mechanisms like landing gears and suspensions)
- Normal modes (Natural frequencies and mode shapes, Complex eigenvalues, preloaded eigenvalues)
- Frequency response analysis (Direct integration and mode based steady-state response analysis)
- Acoustic and NVH analysis (Boundary element based acoustic analysis, fully acoustic analysis)
- Random response analysis and Response spectrum analysis
- Radiated power analysis

Crash analysis
Our analyses
- Crash analysis (Complex structures like a vehicle, mobile phone, ect..)
- Strain-rate dependent materials
- Post-buckling effects
- Explicit dynamic (Complex dynamic structures like crankshafts)
- Blast simulations (soils, fluids and structures)
- Drop test simulations
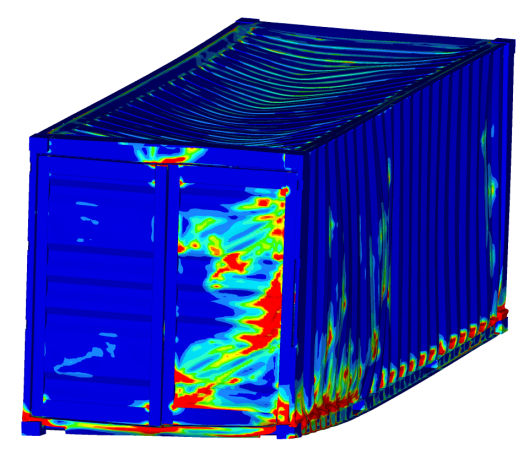
Fatigue
Our analyses
- Static analysis based fatigue (S-N curve, mean stress correction, residual stresses )
- Vibrational fatigue (Based on random response analysis)
- Thermomechanical fatigue (Power electronic thermo-mechanical analysis)
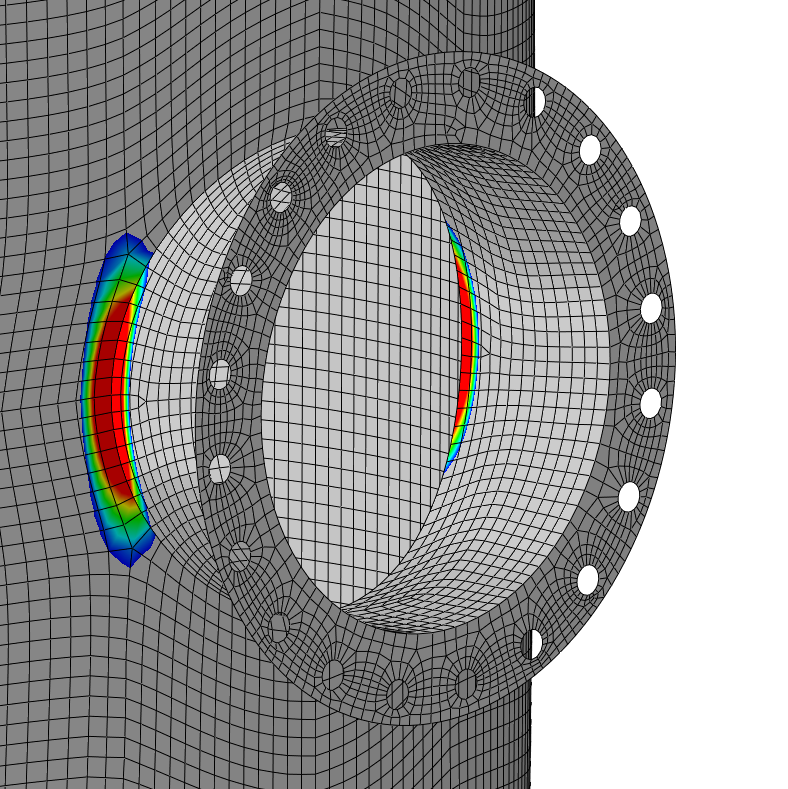
Composite material
Our analyses
- Predictions of components made from high-performance materials
- Inter and intra laminar damage modelling (Ply failure and delamination)
- Multi-scale analysis (Larger structures with embedded domains)
- Impact simulations on laminates (Stacked-shell approach)
- Micromechanics (Homogenization and localization)
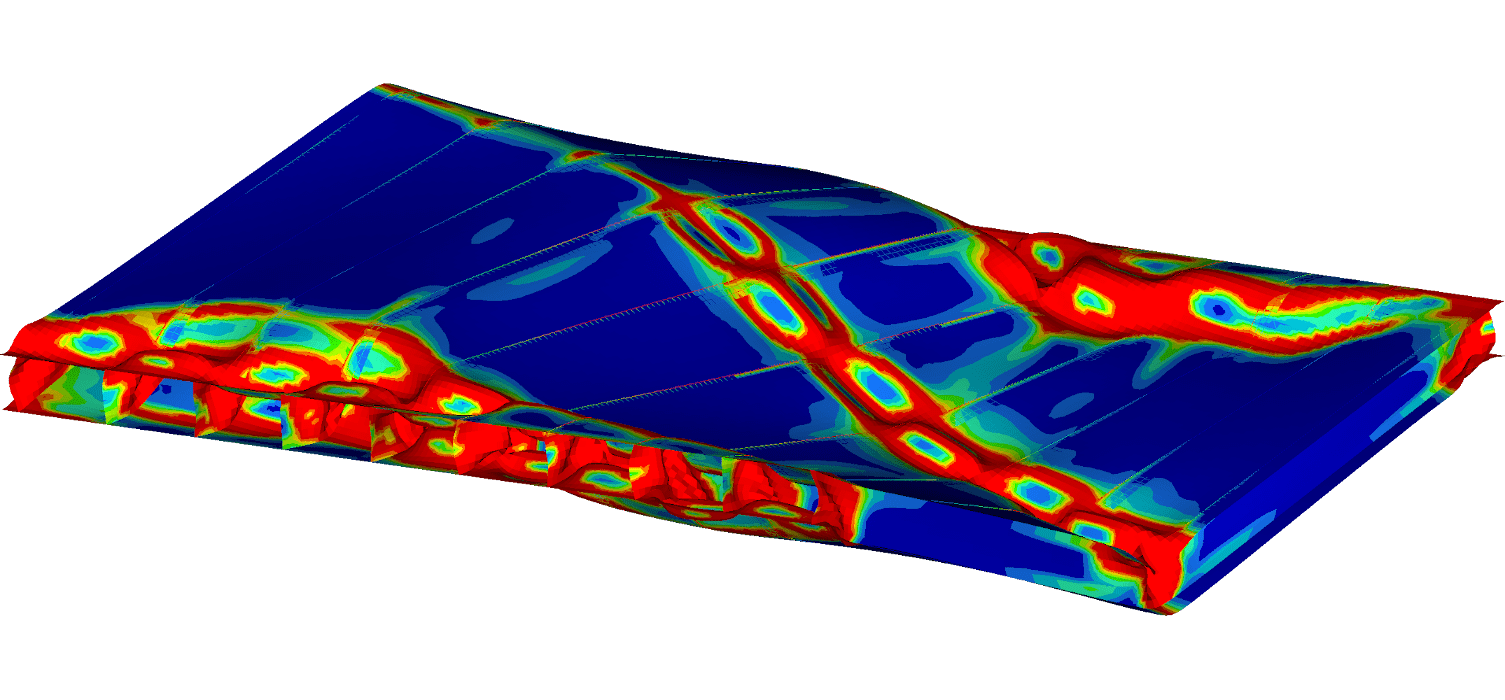
Thermal analysis
Our analyses
- Solid heat transfer (Conduction and Radiation)
- Conjugated heat transfer (Air and Liquid cooling)
- Joule heating (Coupled electric thermal analysis for realistic heat losses calculation)
- Battery cell, electronic and electric motor cooling
- Heat exchanger and boiler thermal analysis
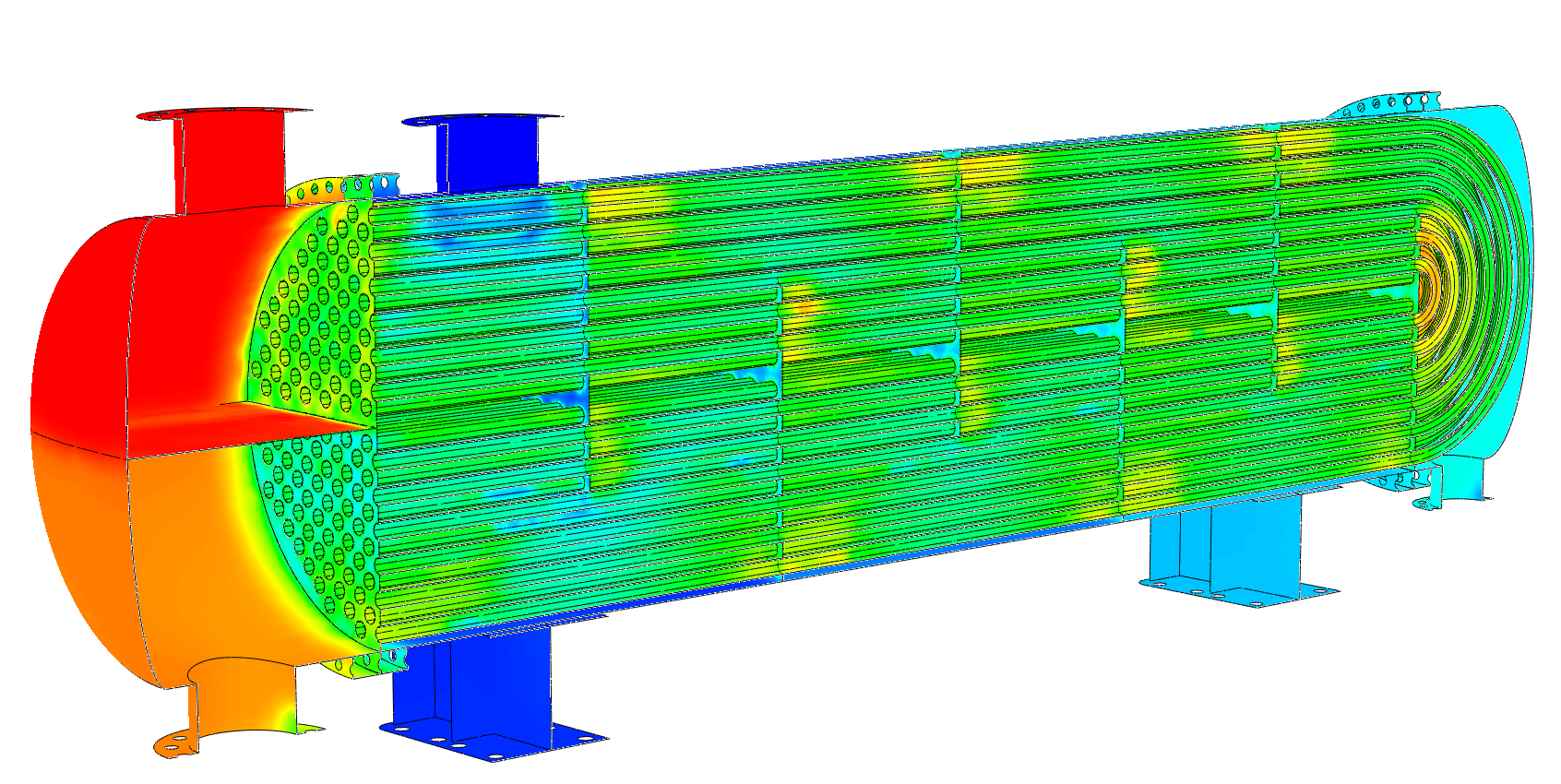
Computational fluid dynamics
Our analyses
- Multiphase flow simulation
- Particle analysis (Smooth particle hydrodynamics)
- Fluid-structural interaction (Turbine loads, exhaust system loading)
- Turbomachinery (pumps and turbines)
- Forced and natural convection
- Free surface flow (Complex shapes of cooling channels)
- Aerodynamics
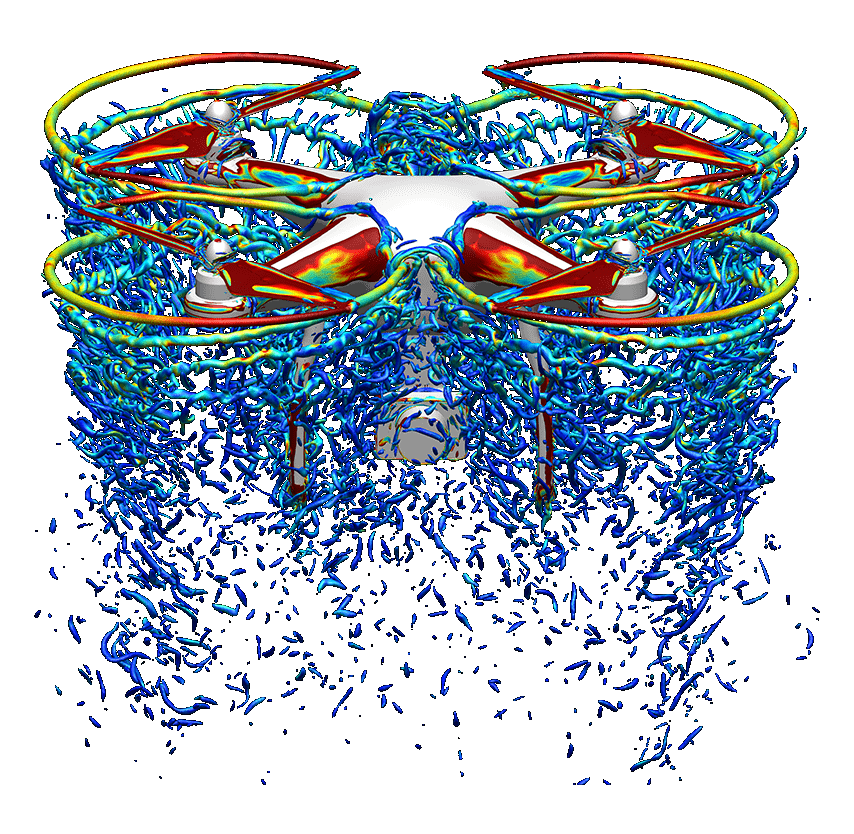
Bulk material analysis
Our analyses
- Discrete element method for bulk analysis
- Complex bulk material models
- Conveyor and hopper analysis
- Bulk material loading extraction
- Ware analysis
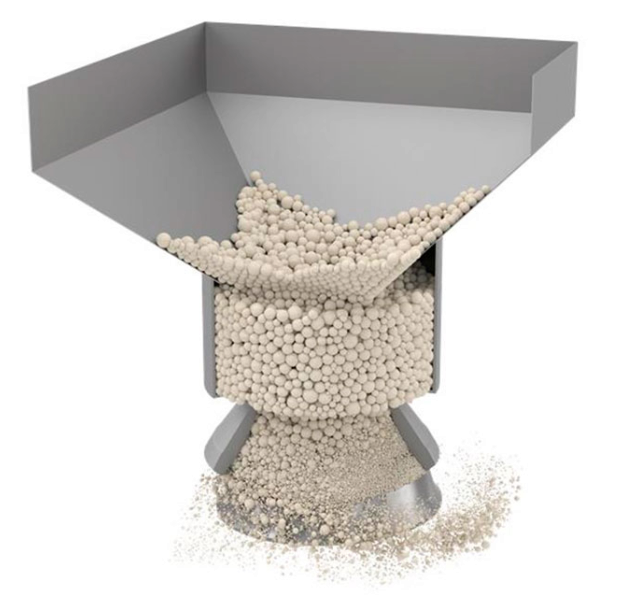
Manufacturing analysis
Our analyses
- Injection molding (Simulation of flow, pack and warping stages. Optimization of cooling and molding parameters for higher productivity)
- Forming (Analysis of deep drawing for single and multi-stage tools. Optimization of the die for the springbuck effect.)
- Casting ( Gravitations, low and high-pressure casting processes)
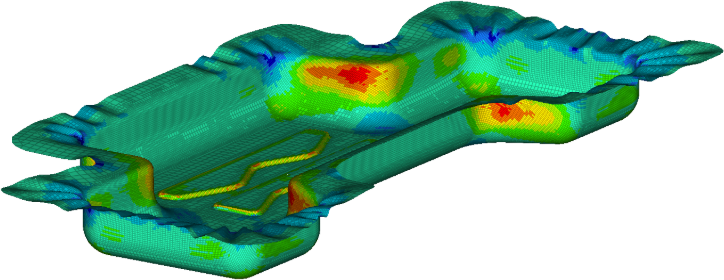
Electromagnetic analysis
Our analyses
- PMSM analysis (Concept design, Torque speed characteristics, Cogging torque, back EMF harmonic study, Id-Iq maps, Eddy current losses, NVH)
- Induction motor analysis (Analysis of entire IM period, study of harmonics, starting analysis)
- SMR motor analysis (switch on-off angle optimization, losses calculation, current chopping techniques)
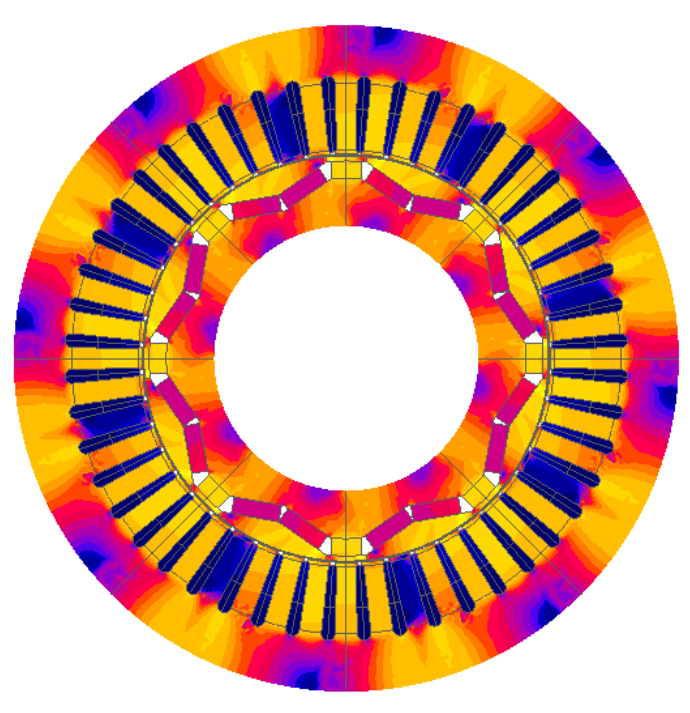
Numerical optimization
Our analyses
- Parametric optimization - (Shape optimization, thickness optimization, composite optimization, material characterization)
- Topology optimization - (Complex design spaces, multi-objective and multi-constraint optimization, manufacturing constraints)
- Topography and shape optimization - (Bead optimization, metal sheet thickness optimization, shape optimization)
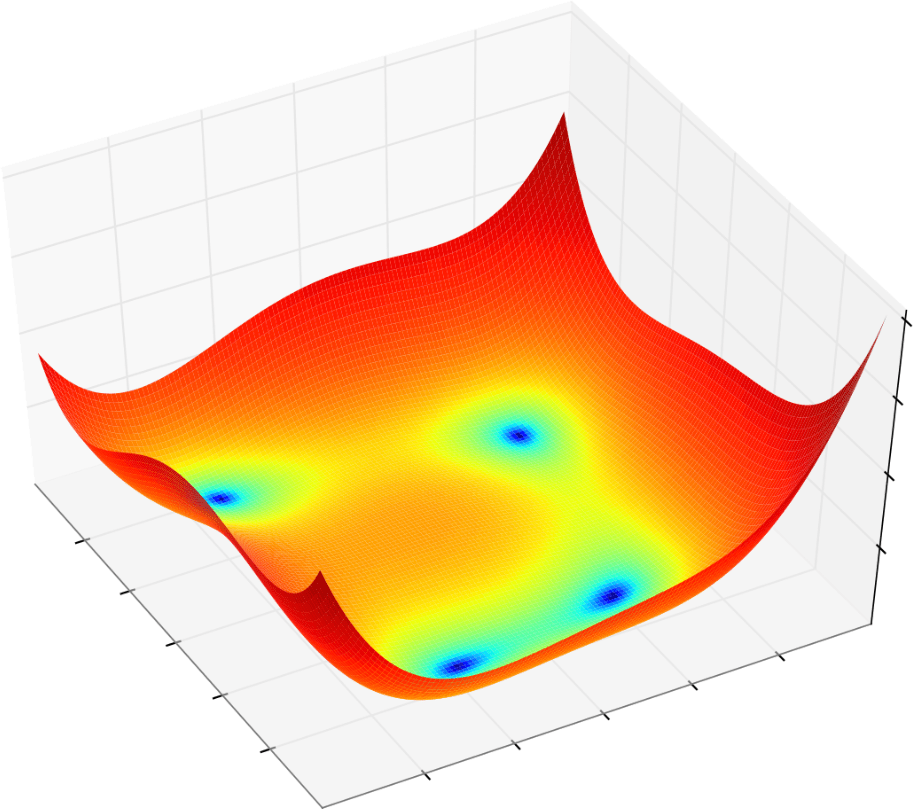